Home >
Galvanization
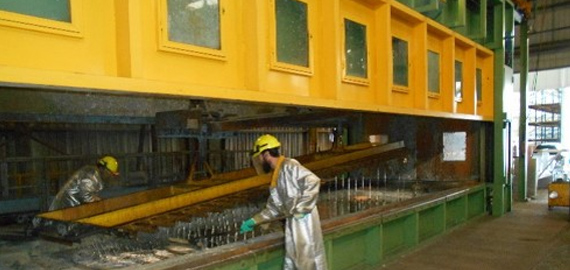
Our offer

Handling with processes

Understanding the processes
Our galvanization’s plants
ZINQ Auvergne
ZINQ Valence
ZINQ Val de Loire
ZINQ Mâcon
ZINQ Bordeaux
ZINQ Lyon
ZINQ Ardennes
AN OFFER DESIGNED TO MEET YOUR NEEDS
Your galvanizing needs are diverse. They concern pieces of all sizes, unique or produced in large series. Your production sites and construction sites are located everywhere in France, in nearby countries or at the end of the world. You want to subcontract the only galvanizing step, or you are looking for a partner who can accompany you from design to delivery on site.
To serve you, the group ZINQ has designed an offer adapted to the variety of your needs :
- Zinc baths for galvanizing pieces from a few centimetres to 16 meter lengths
- Hot dip galvanizing lines by dipping or centrifugation
- Seven factories spread across France without closure
- Logistics solutions tailored to your requirements
- Quality support to enable you to meet all the requirements of your contractors
- Advice and diagnostics are offered by our chemical and metallurgical analysis laboratory
GALVANIZATION IS THE CHOICE OF EFFICIENT AND SUSTAINABLE PROTECTION FOR YOUR STEELS
Are you wondering if galvanizing is the ideal surface treatment for your steels ? Whether you are builders, prime contractors or project owner, we bring you clear answers to your requests and discuss the advantages of this surface treatment. Hot dip galvanizing according to ISO 1461 is the most effective surface treatment for your projects. In order to comply with your specifications, we apply the standards and specifications that govern galvanization.
The ZINQ group gives you access to a wide range of information on :
- The lifetime of galvanizing.
- The advantages of choosing this surface treatment on your steels.
- The standards and specifications we subscribe to.
- All the information we share about surface treatments
DISCOVER THE DETAIL OF THE DIFFERENT PROCESSES THAT WE OFFER
Do you have questions about the process we are doing ? We offer a detailed explanation of the ISO 1461 hot dip galvanizing we perform on all our sites. If you want to visualize this process, we provide you with videos we provide you with videos detailing the successive stages of treatment for the pieces that you entrust to us. You want to entrust us with small parts (bolts, screws) to galvanize ? The method we apply is slightly different. We apply the galvanizing by centrifugation that our sites of ZINQ Val de Loire and ZINQ Ardennes master perfectly. The white rust that builds up on your steels does not satisfy you ? In order to solve this problem, our sites of ZINQ Auvergne and ZINQ Bordeaux offer you the passivation of your parts.
To know our processes in more detail, we inform you on :
- The process of conventional galvanization step by step
- This process explained in video
- The process of galvanizing by centrifugation that will allow you to galvanize your small parts
- Passivation, which helps fight against damp spots.
CHOOSE A PLANT